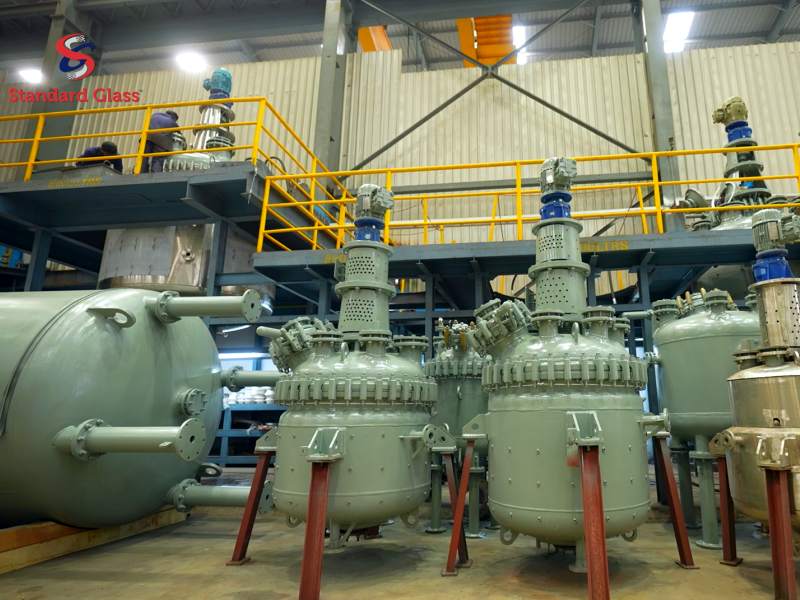
Reactors are extensively used across many industry sectors and specifically pharmaceutical, chemical, food and fertiliser processing plants. They are designed to safely contain chemical reactions and/or thermal changes of ingredient substances in a pressurised environment, acting in a similar way to a pressure cooker in a domestic household kitchen.
If the substances used in the vessel are highly potent, toxic and of a particularly hazardous nature with aggressive chemical reaction affects, glass lined reactors are typically used rather than stainless steel reactors. A glass lined reactor has a hard wearing enamel surface coating on the wetted surfaces which provides high chemical resistance to the vessel – ideal for reactor applications.
After the reaction, the media inside the vessel is then discharged in a number of ways to a variety of subsequent operations including condensing, separation, distillation, evaporation and weighing/packaging. Ultimately the media is sent to a finishing process such as a tablet forming and packing machine or dispensed into bottles and containers for human consumption. In addition to obvious health issues, if the media is not reacted correctly inside the vessel then large amounts of time and money can be wasted by the subsequent process operations. Therefore, in-cycle reactor checking of the media to ensure the reactions are to the correct quality is the secret of a successful process.
Plant designers endeavour to ensure that the substances contained within the vessel react to the correct quality standard and at the highest efficiency. As with any process optimisation the first priority is to ensure safety and quality standards are not compromised. Then, plant designers must aim to produce the highest yield of product while spending the least amount of money to purchase and sustainably operate the reactors.
‘Sustainably operate’ is a key phrase. Above all the normal operating expenses such as energy input, energy removal, raw material costs and labour, is the issue of sustainable stakeholder safety is of paramount importance. Reactor risk management is all about expecting the unexpected and minimising human process intervention helps to mitigate risk and keep operations safe.
Probably the highest risk in the reactor process is taking a process media sample at elevated temperatures. This is major cause of concern for Pharmaceutical plants especially when taking the sample from a Reactor where the reaction is hazardous as found on practically all glass lined reactor applications. Spill over and exposure of sampling liquid is a perennial cause of batch rejection, reprocessing and various quality-related issues ultimately leading to personnel risk and lost profit.
Forward thinking plants are now standardising on reactor sampling systems which are designed to provide automatic vacuum-operated safe sampling.
In India, Standard Glass Lining Technology (SGLT) has sales and service branches located across the country as well overseas in Europe and the UK and are leading the way in this field with their innovative automated reactor sampling device. This device is offered as a value-adding option on their glass lined reactor supply, to ensure they provide their clients with best available practice solutions.
In operation, a pre-established sample quantity is directly pulled into the sampling container by vacuum in a closed-loop manner. At all times, the operator is safe, isolated from the media and in full control. The innovative design is optical sensor powered and is offered with a clear sampling pot so that the operator can see exactly what is happening to the reacted substances at all stages of the reaction process. Furthermore, Distributed Control System (DCS) operation is also possible with the auto sampler and unlike conventional systems, cleaning of the sampling pot is easy, fast and risk-free.
Given the potentially hazardous nature of the substances inside stainless steel, exotic alloy and glass lined reactors, SGLT’s safe auto sampler is now fitted as a site-wide standard by many leading international pharmaceutical manufacturing companies for both new build plants/extensions as well as retro fits to all existing their reactors.
If you believe that your plant would benefit from safe, automatic reactor sampling at all stages of the reactor operation process including elevated temperatures and the use of highly corrosive solvents and aggressive compounds, without the risk of operator exposure, please contact Standard Glass Lining Technology at sales@standardglr.com, Tel: +91 40 2319 5899 or visit www.standardglr.com for further information.
Click here for a downloadable version of this article that appeared in the Chemical Weekly magazine in September 2016