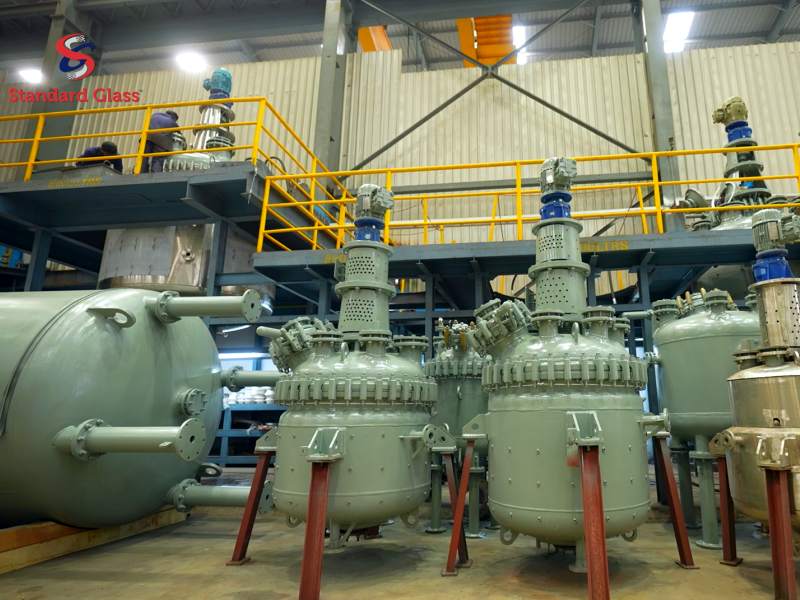
Los reactores se utilizan ampliamente en muchos sectores industriales y, en concreto, en plantas de procesamiento farmacéutico, químico, alimentario y de fertilizantes. Están diseñados para contener de forma segura las reacciones químicas y/o los cambios térmicos de las sustancias de los ingredientes en un entorno presurizado, actuando de forma similar a una olla a presión en una cocina doméstica.
Si las sustancias utilizadas en el recipiente son muy potentes, tóxicas y de naturaleza especialmente peligrosa con efectos de reacción química agresivos, se suelen utilizar reactores revestidos de vidrio en lugar de reactores de acero inoxidable. Un reactor revestido de vidrio tiene un revestimiento superficial de esmalte resistente al desgaste en las superficies mojadas que proporciona una alta resistencia química al recipiente, ideal para aplicaciones de reactores.
Después de la reacción, el medio que se encuentra en el interior del recipiente se descarga de varias maneras para realizar diversas operaciones posteriores, como condensación, separación, destilación, evaporación y pesaje/envasado. En última instancia, el medio se envía a un proceso de acabado, como una máquina de formación y envasado de comprimidos, o se dispensa en botellas y recipientes para el consumo humano. Además de los obvios problemas de salud, si el medio no reacciona correctamente dentro del recipiente, se pueden perder grandes cantidades de tiempo y dinero en las operaciones posteriores del proceso. Por lo tanto, la comprobación de los medios en el reactor durante el ciclo para garantizar que las reacciones son de la calidad correcta es el secreto del éxito del proceso.
Los diseñadores de plantas se esfuerzan por garantizar que las sustancias contenidas en el recipiente reaccionen con el nivel de calidad correcto y con la máxima eficacia. Como en cualquier optimización de procesos, la primera prioridad es garantizar que no se comprometan la seguridad ni las normas de calidad. A continuación, los diseñadores de plantas deben aspirar a obtener el mayor rendimiento del producto gastando la menor cantidad de dinero posible en la compra y el funcionamiento sostenible de los reactores.
Operar de forma sostenible" es una frase clave. Por encima de todos los gastos de funcionamiento normales, como el aporte de energía, la eliminación de energía, los costes de las materias primas y la mano de obra, está la cuestión de la seguridad sostenible de las partes interesadas, que es de vital importancia. La gestión de riesgos de los reactores consiste en esperar lo inesperado y minimizar la intervención humana en los procesos contribuye a mitigar los riesgos y mantener la seguridad de las operaciones.
Probablemente el mayor riesgo en el proceso del reactor es tomar una muestra del medio de proceso a temperaturas elevadas. Esta es la principal causa de preocupación para las plantas farmacéuticas, especialmente cuando se toma la muestra de un reactor en el que la reacción es peligrosa, como ocurre en prácticamente todas las aplicaciones de reactores revestidos de vidrio. El derrame y la exposición del líquido de muestreo es una causa perenne de rechazo de lotes, reprocesamiento y diversos problemas relacionados con la calidad que, en última instancia, conllevan riesgos para el personal y pérdidas de beneficios.
En la actualidad, las plantas con visión de futuro están estandarizando los sistemas de muestreo de reactores, diseñados para proporcionar un muestreo seguro automático accionado por vacío.
En la India, Standard Glass Lining Technology (SGLT) tiene sucursales de venta y servicio en todo el país, así como en Europa y el Reino Unido, y es líder en este campo con su innovador dispositivo automatizado de muestreo de reactores. Este dispositivo se ofrece como una opción de valor añadido en su suministro de reactores con revestimiento de vidrio, para garantizar que ofrecen a sus clientes las mejores soluciones prácticas disponibles.
En funcionamiento, una cantidad de muestra preestablecida se introduce directamente en el recipiente de muestreo mediante vacío en bucle cerrado. En todo momento, el operario está seguro, aislado del medio y en pleno control. El innovador diseño está alimentado por sensores ópticos y se ofrece con un recipiente de muestreo transparente para que el operador pueda ver exactamente lo que ocurre con las sustancias reaccionadas en todas las fases del proceso de reacción. Además, el sistema de control distribuido (DCS) también puede funcionar con el muestreador automático y, a diferencia de los sistemas convencionales, la limpieza del recipiente de muestreo es fácil, rápida y sin riesgos.
Dada la naturaleza potencialmente peligrosa de las sustancias presentes en el interior de los reactores de acero inoxidable, aleaciones exóticas y revestimiento de vidrio, el muestreador automático seguro de SGLT se instala actualmente de forma estándar en muchas de las principales empresas internacionales de fabricación farmacéutica, tanto en las plantas de nueva construcción/ampliación como en los reactores existentes.
Si cree que su planta se beneficiaría de un muestreo seguro y automático del reactor en todas las fases del proceso de funcionamiento del reactor, incluidas las temperaturas elevadas y el uso de disolventes altamente corrosivos y compuestos agresivos, sin riesgo de exposición del operario, póngase en contacto con Standard Glass Lining Technology en sales@standardglr.com, Tel: +91 40 2319 5899 o visite www.standardglr.com para obtener más información.
Haga clic aquí para descargar una versión de este artículo que apareció en la revista Chemical Weekly en septiembre de 2016