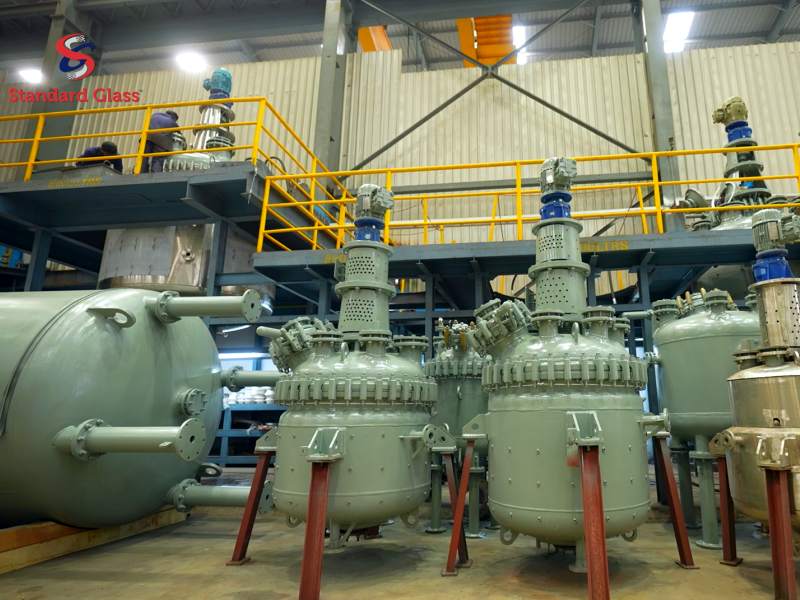
Reaktoren sind in vielen Industriezweigen weit verbreitet, insbesondere in pharmazeutischen, chemischen, lebensmittel- und düngemittelverarbeitenden Betrieben. Sie sind so konzipiert, dass sie chemische Reaktionen und/oder thermische Veränderungen von Inhaltsstoffen in einer unter Druck stehenden Umgebung sicher eindämmen, ähnlich wie ein Schnellkochtopf in einer Haushaltsküche.
Wenn es sich bei den im Behälter verwendeten Substanzen um hochwirksame, giftige und besonders gefährliche Stoffe mit aggressiven chemischen Reaktionen handelt, werden in der Regel emaillierte Reaktoren anstelle von Reaktoren aus Edelstahl verwendet. Ein emaillierter Reaktor hat eine verschleißfeste Emaille-Beschichtung auf den medienberührten Oberflächen, die dem Behälter eine hohe chemische Beständigkeit verleiht - ideal für Reaktoranwendungen.
Nach der Reaktion werden die Medien im Inneren des Behälters auf verschiedene Weise in eine Reihe von Folgeprozessen wie Kondensation, Trennung, Destillation, Verdampfung und Verwiegung/Verpackung entlassen. Schließlich wird das Medium zu einem Veredelungsprozess wie einer Tablettenformungs- und Verpackungsmaschine geschickt oder in Flaschen und Behälter für den menschlichen Verzehr abgefüllt. Abgesehen von den offensichtlichen gesundheitlichen Problemen können bei einer fehlerhaften Reaktion des Mediums im Reaktor große Mengen an Zeit und Geld für die nachfolgenden Prozessschritte verloren gehen. Daher ist die Überprüfung der Medien im Reaktor während des Zyklus, um sicherzustellen, dass die Reaktionen die richtige Qualität aufweisen, das Geheimnis eines erfolgreichen Prozesses.
Anlagenplaner sind bestrebt, sicherzustellen, dass die im Behälter enthaltenen Stoffe in der richtigen Qualität und mit der höchsten Effizienz reagieren. Wie bei jeder Prozessoptimierung muss zunächst sichergestellt werden, dass die Sicherheits- und Qualitätsstandards nicht beeinträchtigt werden. Außerdem müssen die Anlagenplaner darauf abzielen, die höchste Produktausbeute zu erzielen und dabei möglichst wenig Geld für die Anschaffung und den nachhaltigen Betrieb der Reaktoren auszugeben.
Nachhaltig wirtschaften" ist ein Schlüsselbegriff. Neben den normalen Betriebskosten wie Energiezufuhr, Energieabfuhr, Rohstoffkosten und Arbeitskosten ist die Frage der Sicherheit für nachhaltige Interessengruppen von größter Bedeutung. Beim Risikomanagement von Reaktoren geht es vor allem darum, das Unerwartete zu erwarten, und die Minimierung menschlicher Eingriffe in den Prozess trägt zur Risikominderung und Sicherheit des Betriebs bei.
Das wahrscheinlich größte Risiko im Reaktorprozess ist die Entnahme einer Prozessmedienprobe bei erhöhten Temperaturen. Dies ist in pharmazeutischen Betrieben ein großes Problem, insbesondere wenn die Probe aus einem Reaktor entnommen wird, in dem eine gefährliche Reaktion abläuft, wie dies bei praktisch allen emaillierten Reaktoren der Fall ist. Das Überlaufen und die Freisetzung von Probenflüssigkeit ist ein ständiger Grund für die Zurückweisung von Chargen, die Wiederaufbereitung und verschiedene qualitätsbezogene Probleme, die letztendlich zu Personalrisiken und Gewinneinbußen führen.
Vorausschauende Anlagen verwenden jetzt standardmäßig Reaktorprobenahmesysteme, die eine automatische, vakuumgesteuerte und sichere Probenahme ermöglichen.
In Indien hat Standard Glass Lining Technology (SGLT) Vertriebs- und Serviceniederlassungen im ganzen Land sowie in Übersee in Europa und im Vereinigten Königreich und ist mit seinem innovativen automatischen Reaktorprobenahmegerät führend in diesem Bereich. Dieses Gerät wird als wertsteigernde Option für ihre emaillierten Reaktoren angeboten, um sicherzustellen, dass sie ihren Kunden die besten verfügbaren Praxislösungen bieten.
Im Betrieb wird eine vorher festgelegte Probenmenge durch Vakuum in einem geschlossenen Kreislauf direkt in den Probenahmebehälter gezogen. Der Bediener ist zu jeder Zeit sicher, vom Medium isoliert und hat die volle Kontrolle. Das innovative Design ist mit optischen Sensoren ausgestattet und wird mit einem durchsichtigen Probenahmegefäß angeboten, so dass der Bediener in allen Phasen des Reaktionsprozesses genau sehen kann, was mit den umgesetzten Substanzen geschieht. Darüber hinaus ist mit dem automatischen Probenehmer auch der Betrieb mit einem verteilten Kontrollsystem (DCS) möglich, und im Gegensatz zu herkömmlichen Systemen ist die Reinigung des Probenahmetopfs einfach, schnell und risikofrei.
Angesichts der potenziell gefährlichen Substanzen in Reaktoren aus rostfreiem Stahl, exotischen Legierungen und mit Glas ausgekleideten Reaktoren wird der sichere automatische Probenehmer von SGLT jetzt von vielen führenden internationalen pharmazeutischen Produktionsunternehmen als standortweiter Standard sowohl für neue Anlagen/Erweiterungen als auch für die Nachrüstung aller bestehenden Reaktoren eingesetzt.
Wenn Sie der Meinung sind, dass Ihre Anlage von einer sicheren, automatischen Reaktorprobenahme in allen Phasen des Reaktorbetriebs, einschließlich erhöhter Temperaturen und der Verwendung hochkorrosiver Lösungsmittel und aggressiver Verbindungen, profitieren würde, ohne das Risiko einer Exposition des Bedieners, wenden Sie sich bitte an Standard Glass Lining Technology unter sales@standardglr.com, Tel: +91 40 2319 5899 oder besuchen Sie www.standardglr.com für weitere Informationen.
Klicken Sie hier für eine herunterladbare Version dieses Artikels, der in der Zeitschrift Chemical Weekly im September 2016 erschienen ist